Table of Contents
What is Chamba pottery?
Chamba pottery, also known as black pottery because of its color, are household items such as pots, bowls, pans, frying pans, dishes, and more. All of these objects are the result of a mixture of three types of clay extracted in the village of La Chamba in Tolima.
The types of clay used in the manufacture of Chamba pottery are:
- Smooth dark mud,
- Gray sandy clay
- Red clay
The pottery owes its name to its place of origin, the village of La Chamba in Tolima, Colombia.
La Chamba is located on the banks of the Magdalena River in the municipality of Guamo, in the department of Tolima, Colombia. Rice, corn, beans, yucca, sesame, banana, ahuyama, cotton, lemon, mango, guanabana, and passion fruit are also grown in this village.
Chamba pottery rose to prominence between 1953 and 1956, when Carlos Villaveces, then Finance and Credit Minister, purchased land that he later donated for the construction of a craft center.
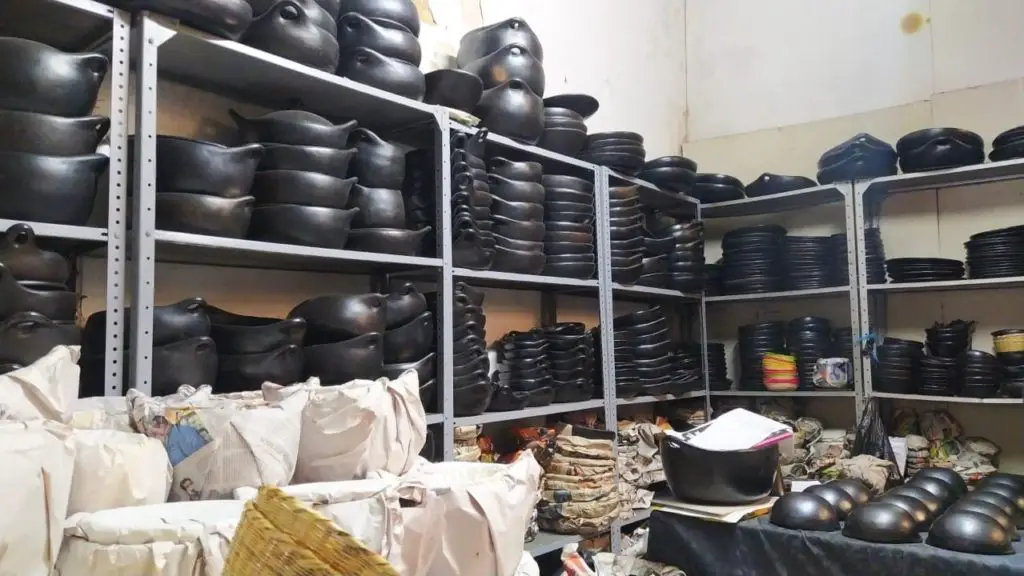
Thanks to the good development of this pottery, La Chamba became a tourist site that today has a theatre, a hotel, a central square, a school, a church, and even a prison.
In addition, in 2005, a handicrafts exhibition center was set up on a part of the central square, the protagonists of which are hand-made pottery.
History of Chamba pottery
The manufacture of Chamba pottery dates back to around 300 years ago, when the ancestors, the Poinco or Yaporogo peoples of the Pijao culture, made vessels for ceremonial purposes or for domestic use in transporting crops and cooking.
The process of making these objects was to collect the earth, mix it to make the dough, and then shape the piece to fire in wood-fired ovens.
This tradition was passed from generation to generation, so at the beginning of the 20th century, it was very common that the pieces still had features or surface treatments similar to those of the pioneers of this type of pottery.
Over time, however, some of these characteristics disappeared and the generations that adopted this practice retained only some forms and the technique of red clay engobe.
With the opening of the road between La Chamba and El Espinal in 1937, Chamba pottery gained national recognition and the artisans began to produce numerous pieces for domestic use, which were sold in different parts of the country.
The motivation to continue this fantastic pottery workshop led to the construction of the La Chamba technical training center in 1972 with the aim of teaching young people the pottery trade.
In the years that followed, the artisans received support from state institutions to continue and maintain this beautiful work.
Today, just over 85% of La Chamba’s population is dedicated to making this type of pottery. It is common for residents of all ages to make these works of art.
It is important to note that from the beginning of Chamba pottery, women were the ones who made the objects. In their hands lies the magic of making all kinds of ceramic objects and they are the ones who prepare and transmit this art to people.
Representative Pieces
As previously mentioned, emblematic pieces have been preserved and produced since the early days of pottery in Chamba to this day. Let’s get to know them!
The Múcura
It is a medium-sized piece, characterized by its shape, which is believed to represent a pregnant woman.
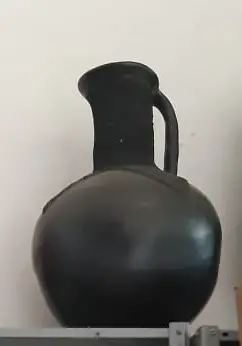
The múcura was used by workers to transport water or other liquids.
The Olla
This is the most famous piece of pottery in the whole country as it is used in the preparation of all the delicious dishes that are typical of every place in Colombia.
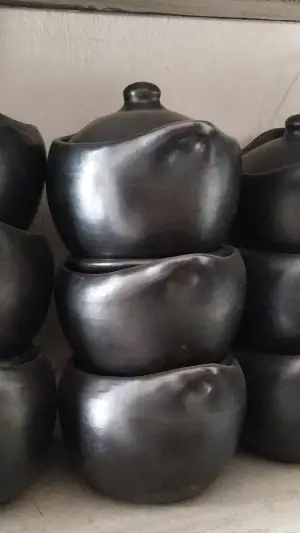
The Olla is characterized by its oval or round shape, but it has a flattened base to allow it to stand firm and steady. They come in different sizes, some have handles and lids.
Clay chickens
As the name suggests, this is a sort of round chest in the shape of a chicken, flat on the bottom and with a lid.
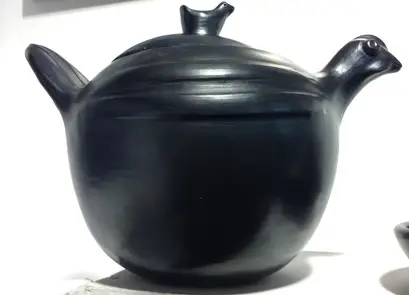
This piece is part of an old tradition where it was given to little girls to play with. Inside the chickens were 12 other small pieces: múcura, olleta, glass, pot, vase, cup, casserole, tray, plate, basket, a toy shaped like a bird, and budare, a piece resembling a frying pan.
The Mohan
It is a mold that requires a lot of work as it is modeled by hand. The Mohán is considered the spirit of the river.
The figure of Mohán is modeled sitting on a stone and smoking tobacco.
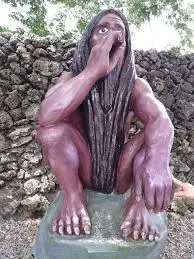
Thanks to the proximity to the river, figures such as fish, bowls and molds with lids in the shape of catfish are also made.
The sun goddess
It was made by the master Ana María Cabezas, who has won national craft competitions, making the piece a famous symbol of Chamba pottery.
The 3 clays for making Chamba ceramics
As mentioned at the beginning, Chamba pottery is made from 3 types of clay: smooth clay, gray sandy clay and red clay. But where do these clays come from?
Smooth dark and sandy gray clay
Both of these species are mined from municipal mines located just outside of La Chamba town center.
These mines are owned by the Tolima government but are in the process of being handed over to the community.
Red Clay
The red clay is quarried in a private mine in the municipality of Suaréz. However, to get there you have to cross the river Magdalena or go there by road.
The red mud is paid for in bundles and then taken to La Chamba in sacks.
It is the men who are in charge of extracting these muds and in order to be able to select the best mud they must have previous knowledge and experience.
Process of elaboration
There are three types of Chamba pottery: black, red, and rustic or unglazed. The step-by-step process of making these three types of pottery is explained below.
- The clays are extracted from various places of origin.
- The clays obtained are transported in sacks to the various workshops. When they arrive at the workshops, they are laid out in the sun to dry.
- They are then crushed by hand using mechanical mills or a wooden pestle.
- The dough to be shaped or modeled is then prepared. Typically, La Chamba artisans mix about 60% sandy clay, 40% smooth clay, and water.
- The clay mixtures are then kneaded. This step involves dumping the sandy clay on the table and adding the previously mentioned amount of smooth clay. Then knead until the mixture is homogeneous.
- Molds are made or the piece is shaped using the different molding techniques that we will discuss later. In this step, the craftsman or potter should always add the amount of dough he deems necessary for the size of the object to be made.
- Once the pieces are made, they are dried at room temperature and in the sun.
- The paint is applied. This process is carried out approximately 12 hours after the workpiece has been finished and dried, whereby the workpiece must still be damp so that the paint can adhere well to the workpiece. The varnish is applied with a brush, usually 3 layers are applied, with an interval of 30 minutes between each layer.
- The paint is dried at room temperature. The piece should not be left in the sun as it may dry out and become hard, making it impossible to polish.
- Polishing is completed. This step checks that the piece is already at least 80% dry. After that, it is rubbed with agate stones, small colored stones extracted from volcanic rock, to remove impurities from the items. The piece is then rubbed with a plastic bag to make it shine.
- The varnish is applied again and left to dry at room temperature.
- The piece is then placed in the sun for a few hours to preheat.
- A large metal or earthenware basket (moyones) is placed in the wood-fired kilns, into which the Chamba pottery pieces are placed. Pieces of ceramic are also added in this step to prevent the pieces from directly contacting each other.
- Then the pieces are placed in the wood stove to be fired, the number of pieces depending on the size of the stove. It is important to know that the temperature at which the pieces need to be fired also depends on their size. Normally the objects are exposed to a maximum of 700ºC.
- When the oven has reached this temperature, the basket with the pieces is removed. To remove them safely, the baskets are pulled out on rods with metal hooks.
- After taking out the objects, they are red and if you want to leave them that way, that’s no problem. However, the most representative feature of Chamba pottery is its distinctive black color, which is obtained through the process of blackening. The blackening is achieved through the use of cagajón (donkey or horse manure), previously treated to eliminate impurities, or through the most commonly used material, rice husks.
- For the blackening process, you have to wait about 10 to 15 minutes before covering the container and then adding the cagajón or rice husks without removing the items. This process is achieved by burning the pieces due to the high temperatures inside the container, which impregnates them and gives them this color.
- Then the caneca is covered and the pieces are gently shaken so that they move inside and acquire the black color.
- After the pieces have been properly colored, they are placed back in the oven to take advantage of the remaining heat and fully cook the pieces.
- If you want to leave your piece without blackening, you should continue with blueing after you have varnished your object. This process uses an agate stone to remove imperfections while giving the piece a shine that retains the clay’s natural color.
Techniques for modeling Chamba pottery
To create Chamba pottery, potters use modeling and molding techniques that have long been used in the pottery world. These techniques are as follows:
Modeling
Modeling consists in sculpting a character for the first time and it involves the following techniques:
Modeling by hand
In this technique, the clay is modeled with both the fingers and the palm of the hand. This is the oldest technique as no other molding tools are used.
Millions of shapes can be made with hand modeling and for Chamba pottery, it is optimal for creating the little chickens, the ears of the pots or casseroles, and the decorations.
Coiling
This modeling technique consists of clay cylinders placed one on top of the other to create long and large objects.
Rolling is ideal for making items such as vases and jars.
Pinching
Pressing involves forming a ball of clay and then pressing it with your fingers so that it becomes elongated and narrow towards the bottom but wide towards the top.
This technique is ideal for thinning the walls of the piece being made and is typically used for making the bases of items.
Molding
Molding is the removal of molds from parts that have already been manufactured. This is the most important technique in the manufacture of ceramics because if you master it, you can make the pieces in less time.
To make the shape, the dough must be kneaded very well, then dry clay is sprinkled on the surface where the dough is to be spread, giving it the shape of an arepa (corn cake) of the desired thickness.
Then this layer is placed on an object or mold to give it shape with the help of bamboo spoons. Finally, the excess clay is cut off.
The following techniques are used in shaping:
Molding on clay
This technique uses clay molds on which the dough is placed, which then takes on the shape of the mold below.
Usually, the molds are made in the same workshops. There are potters who use a potter’s wheel, but there are also those who don’t need this tool because they are all experts!
Molding on other materials
This technique does exactly the same thing, except that the object that is placed under the dough is not a shape, but an ordinary object like a rock or turtle shell.
This technique is ideal for making objects that can have unique shapes and sizes, such as B. Totoumos, or for making molds for these objects.
Finishings of the Chamba pottery
The finishing is the last step that the potter takes to finish his pieces and give them a beautiful touch.
Although they are mentioned in the steps of making pottery, let’s see how they are applied to making Chamba pottery.
Varnishing with red clay
The first finish is the red clay varnish so that it retains this color. To apply this finish to a piece of Chamba ceramic, the following steps must be followed:
- Dry the red clay at room temperature.
- Pulverize or grind the clay. This is done with special machines or by hand with the help of a wooden pestle.
- Sieve the pulverized clay to remove any impurities.
- Hydrate with water until a red varnish is formed.
- Once the parts are ready, using a brush, apply 3 coats with a 30-minute break between each coat.
- Finally, the pieces are laid out in the sun to dry.
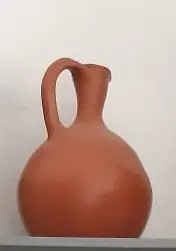
Brushing
The second finish we’re going to talk about today is polishing. This technique consists in polishing a lacquered piece. This process is carried out in the following two simple steps:
- Allow the workpiece to dry on 80% of its surface.
- Agate stones or semi-precious stones are rubbed all over the piece to add shine and to close the pores or holes of the piece.
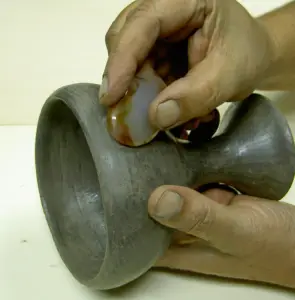
The ideal kiln for the Chamba pottery production
We continue with one of the most important and indispensable tools for the production of any type of ceramics, the kiln.
There are different types of kilns, but today we want to focus on the kiln used by the potters who make Chamba pottery. The wood-fired kiln is the kiln of choice for many potters making Chamba pottery.
This type of oven is built by a professional who has spent his whole life in this profession because it must be perfectly made to be used without problems. The wood-fired oven is made of clay and is very large. It is usually up to 2.5 meters high and can be up to 3 meters in diameter.
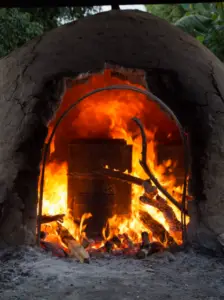
Its size is ideal for placing the baskets with the pieces inside. It is interesting that this kiln does not have a door like the other kilns, because through an entrance that is kept open, the potters take out the baskets without running the risk of burning them.
The firing time for about 20 pieces is two to three hours at temperatures between 700ºC and 750ºC.
After this, the pieces are taken out and left in their natural color if desired, otherwise they are subjected to the blackening process described above.
The most used tools for making Chamba pottery
As with all processes of making clay objects, there are tools that facilitate the creation of Chamba pottery.
We will now give you a list of these must-have tools for this process.
- Corn husk
- Totumo spoon
- Plastic spoon
- Bamboo Profiler
- Potter’s wheel
- Brush
- Sponges
- Clay molds
All of these tools are made of materials that will not damage the pieces made by the potter. For more information, visit our blog about pottery tools.
Celebrations of Chamba pottery
You probably didn’t know that because the art of pottery plays an important role not only in Tolima but also throughout the country, there are some festivals that celebrate the work of potters and the pottery art as a traditional and artistic practice. Do you want to know what those are? Just keep reading.
Mud fair
The mud festival is held every two years in La Chamba, Tolima, Colombia. This festival was created about 16 years ago to recognize the hard work of all the artisans in the area and to popularize this practice across the country.
The festival lasts four days and features all kinds of activities: horseback riding, floats, folk dances, craft demonstrations, competitions and activities for children, youth, and adults, and the most popular event of all: the Youth and Children’s Regency.
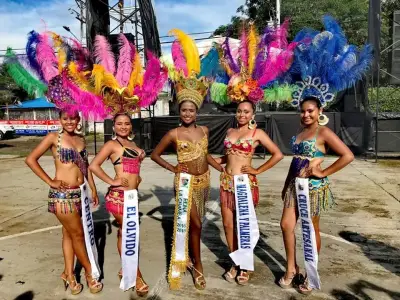
It consists in electing the representative of La Chamba for the next two years. To win, the contestant must demonstrate not only her beauty but also her skills as a Sanjuanero dancer and craftsman. This shows that the Chamba pottery is undoubtedly passed down from generation to generation.
The great thing about this event is that it is completely free and suitable for viewers of all ages. However, there are no official dates for the festival as it takes place every 2 years in different months.
The last Mudfest was in 2018 and Vanessa Barragan was crowned Miss Chamba.
Website: https://www.tolima.gov.co/
Manos de Oro Craft Exhibition
As part of the celebrations of the Festival del Barro also takes place the Muestra Artesanal Manos de Oro instead.
Visitors can take part in activities such as B. donkey races and mud wrestling.
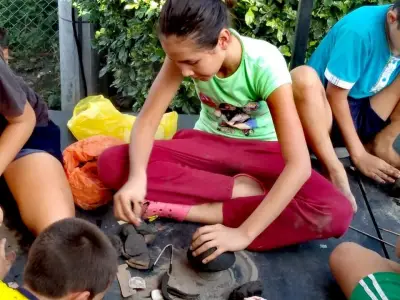
Where to see Chamba pottery in Colombia
We recommend viewing this type of pottery in La Chamba or in the municipality of Guamo in Tolima. There you can follow the entire manufacturing process and visit the numerous workshops.
We also recommend that you visit the stand in the central square of La Chamba, where not only can you admire the beautiful creations and their workmanship, but you can also buy the pieces you want to take home with you.
If you are in Bogotá, we recommend visiting the Artesanías de la Chamba workshop in La Candelaria, a historic area of the Colombian capital.
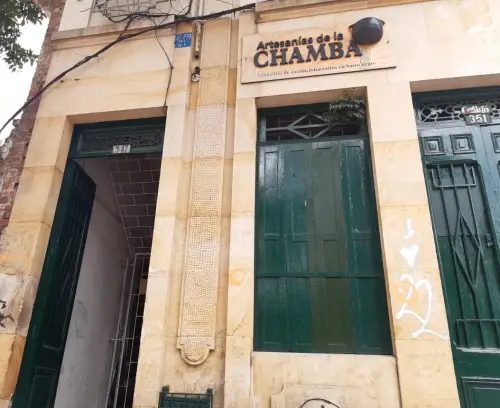
We recently had the opportunity to visit this place and we left totally inspired with the sole intention of continuing to learn about this practice and sharing this fantastic work with all of you.
As soon as we walked in, the owners welcomed us with open arms and told us everything there was to know about Chamba pottery and were always ready to answer our questions.
In the workshop, you can see hundreds of emblematic Chamba pottery items, all stored and packaged for export to the United States. Amazing, isn’t it?
Address Chamba Workshop Bogota: Calle 16 # 3-47, La Candelaria, Centro.
Explore this complete Colombia Travel Guide and find all the information you need to get to know Colombia as a tourist destination.
Importance of Chamba pottery in Colombia
Chamba pottery represents culture, traditions, the hard work of the artisans, but above all the creativity and talent of Colombian artisans and potters. For this reason, in 2019 it received the recognition with the Designation of Origin ” Artisan ” conferred by the Superintendence of Industry and Commerce of Bogotá.
It is also worth emphasizing that it is a source of income for the country, which, unfortunately, is not as recognized as in other markets.
It is important that Colombians are proud of this ancient and artisanal practice and are interested in supporting Colombian artisans to honor their talent, dedication, and originality, which are a source of pride for the country.